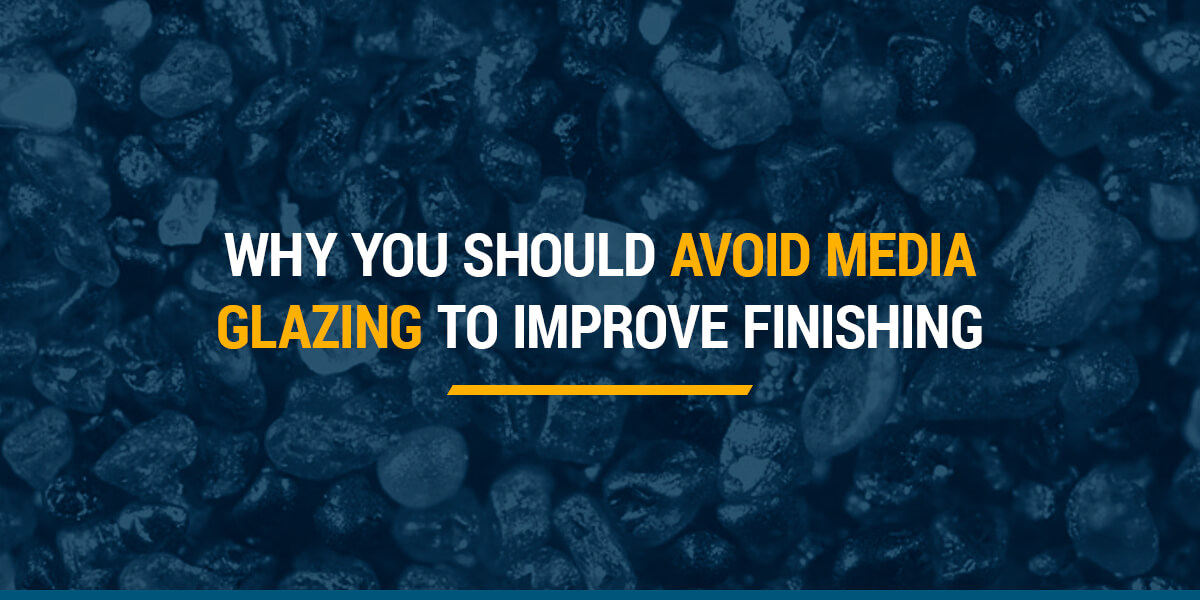
Why You Should Avoid Media Glazing to Improve Finishing
Updated: March 12, 2024Abrasive media plays a crucial role in surface finishing across various industries. From deburring and polishing to cleaning and burnishing, different types of media—such as ceramic, plastic, and steel—are used to achieve the desired finish on workpieces. However, over time, a common issue known as media glazing can occur, reducing the effectiveness of the media and leading to inconsistent results. Understanding what causes glazing and how to prevent it is essential for maintaining high-quality finishes and meeting customer expectations.
What Is Media Glazing?
Media glazing happens when fine metal particles and debris from the workpiece accumulate on the surface of the abrasive media during the finishing process. This typically occurs in vibratory finishing machines where friction between the workpiece and the media helps remove imperfections. As these particles build up, they coat the media, reducing its ability to cut or polish effectively. Instead of delivering a clean and uniform finish, glazed media may leave behind an uneven or burnished surface, and even transfer contaminants to the workpiece itself.
The consequences of media glazing can be significant. It often leads to longer cycle times, reduced productivity, and lower quality outputs. By avoiding glazing, you can maintain consistent throughput, reduce rework, and ensure that your finishing processes meet the standards your customers expect.
What Causes Glazing?
Several factors can contribute to media glazing. The most common ones include:
- Compound concentration: Using too little compound can prevent proper cleaning of the media, increasing the risk of glazing.
- Water flow: Inadequate water flow fails to flush out metal particles, allowing them to accumulate on the media.
- Part-to-media ratio: A high ratio, especially with oily or greasy parts, can lead to faster glazing.
- Media size: Small media can clog drains, trapping dirty water and causing glazing.
6 Tips to Prevent Media Glazing
To keep your media performing at its best, follow these practical steps:
1. Use the Right Compound for Your Material
Softer materials like copper, brass, aluminum, and certain steels are more prone to glazing. Selecting the appropriate compound for your equipment and workpiece material ensures better results and prevents unwanted buildup.
2. Maintain Proper Compound Concentration
Ensure you're using the correct concentration—usually between 0.7% and 1%—based on your system’s water volume and capacity. Too low a concentration can lead to glazing and extended cycle times.
3. Keep Drains Clear
Clogged drains can trap contaminants and cause glazing. Regularly check and clean your drains, or consider frequent water changes if your system requires closed drains.
4. Ensure Adequate Water Flow
Good water flow helps remove debris and keeps the media clean. Open drains with sufficient flow produce the best results, ensuring a cleaner environment and more consistent finishes.
5. Monitor Your Wastewater
Dark or concentrated wastewater can signal issues such as poor metallurgy, high part-to-media ratios, or excessive oils. Regularly analyze your wastewater to identify and address problems early.
6. Check and Replace Media as Needed
Over time, media can degrade or become too small for the process. Implement regular checks and replace any media that shows signs of glazing or wear to maintain performance.
How to Restore Glazed Media
If your media has already started to glaze, don’t throw it away just yet. You can restore its effectiveness by adding an abrasive cleaning powder and running the tumbling machine for several hours. Afterward, rinse the media thoroughly to remove any residue. This method is cost-effective, especially if a large portion of your media is affected.
Get in Touch With Finishing Systems Today
Media glazing may seem like a minor issue, but it can have a major impact on your finishing results. Fortunately, there are effective ways to prevent it and restore your media when needed. At Finishing Systems, we specialize in providing solutions to help you achieve consistent, high-quality finishes. Contact us online today to learn more about media glazing or ask questions about our products and services.
Explosion Proof Type Pyrometer
This classification includes pyrometers designed for blast furnace equipped with explosion proof instrument.
Conditions in furnace are always tough alone with high temperature and high pressure. Limited to the requirements of operation environment and instrument`s structure, thermocouple thermometry would result in inaccurate measurement and lag reaction when works in harsh condition such as frequently temperature changes, large pressure fluctuations and event in vibration.
Since a thermocouple works at the high temperature ( usually 1200 ℃ ~ 1300 ℃) in furnace for long term, the thermocouple junction box also works at high temperature between 100 ℃ to 120 ℃, which will dramatically reduce instrument`s service life to a range from few weeks to few months. It will increases use-cost and maintenance workload.
In order to overcome above shortcomings, our company has designed and produced a serials of specialized infrared temperature measure device to ensure our infrared temperature measuring system works reliably in complex environment.
Explosion Proof Type Pyrometer,Explosion Proof Pyrometer,Stove Use Pyrometer,Pyrometer For Industry Furnace
Changzhou Sijie Optoelectronics Technology Co.,Ltd. , https://www.sjinfrared.com