Manufacturers Discover the Advantages of Laser Brazing
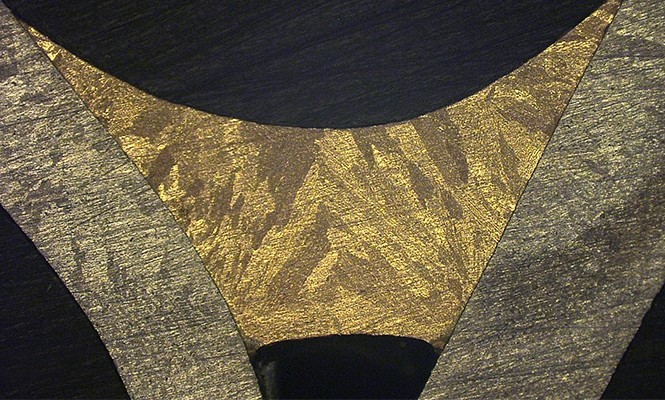
As more manufacturers explore advanced joining techniques, laser brazing is emerging as a game-changer. This cutting-edge process not only offers superior precision and efficiency but also brings new levels of flexibility and cost savings to metal assembly operations.
If you're looking for a reliable and efficient method to join metals without compromising quality, laser brazing could be the solution you’ve been searching for. Let’s dive into how this innovative technology is reshaping the manufacturing landscape.
Why Brazing Outperforms Welding in Many Applications
Brazing is a highly effective technique for joining metal components, especially when traditional welding methods fall short. Unlike welding, which melts the base material, brazing uses a filler metal that is melted and flows into the joint to create a strong bond. This distinction allows for the joining of dissimilar metals, opening up new possibilities in design and material selection.
Another major advantage of brazing is the lower heat input compared to welding. This reduces the risk of warping or distortion in sensitive components. Additionally, because less material is required and fewer steps are involved, overall costs can be significantly reduced.
Traditional brazing methods include torch brazing, arc brazing, furnace brazing, and induction brazing. Each has its own applications, but they all share the same core principle: using heat to melt a filler metal and form a strong joint.
How Laser Brazing Enhances Precision and Efficiency
Laser brazing takes the advantages of traditional brazing to the next level by introducing high-precision control. Using fiber laser technology, the process delivers consistent, accurate results with minimal heat affecting the base materials. This leads to faster production cycles and higher throughput.
One of the key benefits of laser brazing is that it doesn’t require flux, further reducing material and labor costs. The elimination of excess heat also helps maintain the integrity of the joined parts, making it ideal for delicate or high-tolerance assemblies.
Fiber lasers used in this process are solid-state systems, meaning they require very little maintenance and offer long-term reliability. With features like hot-swap redundancy, manufacturers can ensure continuous operation and minimize downtime—critical factors in industrial settings.
Laser brazing also integrates seamlessly with automation. Robotic systems can precisely control both the laser’s firing and movement, ensuring consistent, repeatable joints. This eliminates human error and ensures every weld is identical, improving quality and reducing rework.
Industries such as aerospace, automotive, and medical device manufacturing are increasingly adopting laser brazing due to its precision, speed, and cost-effectiveness. Companies like Genesis Systems provide tailored laser solutions to meet the unique needs of these sectors.
Posted in Laser Welding, Robotic Applications, Robotic WeldingInjection Machine Electric Motor
Injection machines, at the core of plastic molding processes, rely heavily on powerful and precise motors to function efficiently. Among these motors, the injection machine electric motor has emerged as a superior option, offering numerous advantages and unique characteristics compared to traditional hydraulic motors.
The electric motor for injection machines boasts exceptional energy efficiency. By converting electrical energy directly into mechanical power, electric motors eliminate the need for hydraulic pumps and valves, which often result in energy losses through heat generation and fluid friction. This efficiency translates into lower operating costs and reduced environmental impact, making electric motors a sustainable choice for injection molding operations.
Moreover, electric motors offer precise control over the injection process. With advanced electronic controls, electric motors can be programmed to deliver precise torque and speed profiles, ensuring consistent and repeatable injection cycles. This precision enhances the quality of the molded parts, reducing defects and improving overall product consistency.
In addition, electric motors are quieter and more compact than hydraulic motors. The elimination of hydraulic pumps and the associated fluid noise results in a quieter workspace, improving operator comfort and reducing noise pollution. Furthermore, electric motors have a smaller footprint, enabling manufacturers to save valuable floor space in their facilities.
Compared to hydraulic motors, electric motors for injection machines offer superior responsiveness. Electric motors have a faster response time, enabling them to adjust to changes in injection pressure and speed more quickly. This responsiveness is crucial in injection molding, where rapid adjustments are often required to maintain optimal process conditions.
Moreover, electric motors are easier to maintain and have a longer lifespan than hydraulic motors. With fewer mechanical components and less wear and tear, electric motors require less frequent maintenance and repairs. This reduces downtime and operational costs, enhancing the overall profitability of injection molding operations.
Furthermore, the integration of electric motors with advanced technologies such as sensors and control systems enables injection machines to achieve higher levels of automation and digitization. This technology integration enhances the flexibility and scalability of injection molding operations, enabling manufacturers to adapt to changing market demands and produce a wider range of products.
In conclusion, the injection machine electric motor offers numerous advantages over traditional hydraulic motors. Its energy efficiency, precision, quietness, compactness, responsiveness, ease of maintenance, and integration with advanced technologies make it a superior choice for injection molding operations. As manufacturers continue to seek ways to improve efficiency, reduce costs, and enhance product quality, the electric motor for injection machines will likely become an increasingly popular option in the plastics manufacturing industry.
Injection Molding Electric Motors,Electric Drives For Molding Machine,Powerful Electric Drive System for Plastics Molding,Reliable Electric Injection Molding Machine
Ningbo Outai Plastic Machinery Technology Co.,Ltd , https://www.outacmachine.com